Not a day seems to pass without hearing debates and speculations about the future of cars such as electric vehicles (EVs), autonomous driving and so on. There is so much excitement surrounding the field that it sometimes described as a media frenzy. What will emerge and spread? Who will lead the way? The picture is still unclear, but the technology has the potential to redefine the very idea of automobiles and transform the car industry as a result. The competition is fierce, and the interest in the unfolding development is great.
It is with this backdrop that I heard a presentation given at Nagoya University that has made me realize that one thing is going to be crucial no matter what shape the future car takes: the technology make the body of vehicles as light as possible. The lighter the car, the better its fuel efficiency will be. This is particularly important for EVs, with the currently available batteries weighing several times more than combustion engines. A lighter body means a better driving range, which means that lightweight materials may be the star behind EVs.
One of the main contenders to the stardom is a range of carbon fiber composites. Carbon fiber was invented in Japan, and three Japanese companies have around 60% of the world market share. The material is known for being "stronger than iron and lighter than aluminum," and may eventually, it is hoped, to replace metals. The main obstacles are the cost and the problem of processability. Over the last half a century, the applications of this material widened gradually from fishing rods to golf clubs and other sporting equipment, and then to the aerospace industry. Ten years ago, the march of carbon fiber reached a high point with the development of Boeing 787, which uses carbon fiber for half of its airframe. The introduction of carbon-fiber structural members in mass-produced vehicles would mean the mainstreaming of carbon fiber as an alternative to metals. This, however, requires a huge leap in technological development to bring the cost down dramatically. This is the battlefield chosen by the team led by Meidai, which also involves industry partners. It is a battle the team cannot lose, with the future of Japanese car industry at stake.
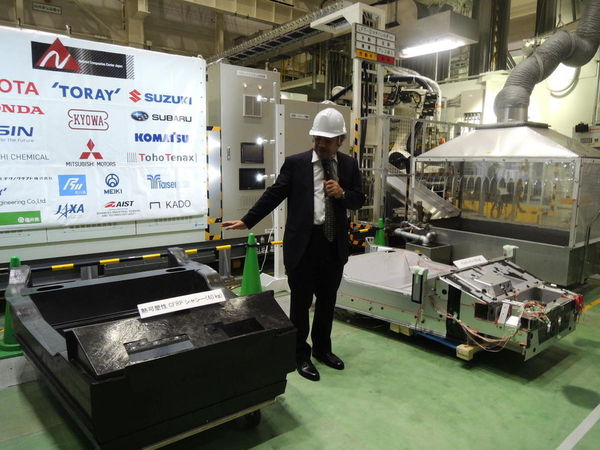
CFRP chassis presented (front) and the aluminum car it was modeled on (at Meidai NCC, October 16, 2017)
In mid-October, the National Composite Center (NCC) at Nagoya University announced that it had succeeded in producing an automobile chassis in a mere minute by compression-molding a carbon fiber-reinforced plastic (CFRP) material in a large press. Although a practical method of using heat-cured resins mixed in with carbon fiber had already been developed, it was a slow process, needing six minutes and more to cure. This time, a heat-softened resin was used instead. Although this requires more precise temperature control, it cuts the processing time drastically. This, apparently, was the first automobile chassis ever made using this method in the whole world. The chassis was modeled on the lightweight aluminum chassis of a sports car, which was 30% lighter than its steel counterpart at 45 kg. The use of CFRP slashed the weight by a further 10% to 40 kg......>>read more on the Meidai Watch
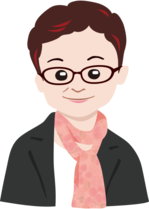 |
Atsuko Tsuji: Earned B.A. in Arts, College of Arts and Sciences, the University of Tokyo in 1976. Joined The Asahi Shimbun Company in 1979 as a journalist and wrote many articles in science and technology area for newspaper and magazines published by the company including editorial pieces. Knight Science Journalism Fellow at Massachusetts Institute of Technology in 1989 and Reuters Fellow at University of Oxford in 2014. Designated Professor of Nagoya University's Institute of International Education and Exchange since October 2016.
|